(uw) 11. Februar 2023 – Besuch bei der Firma BMZ Germany GmbH in Karlstein
Schon länger wollte ich mir die Fertigung von Batterien, besonders den Bau von Batteriespeichern, anschauen. Es gibt zwar viel Infomaterial im Netz und allerlei Prospekte von Herstellern, aber so ganz nah hinschauen ist doch anders.
Es freute mich sehr, dass mich Frau Landgraf, die Pressesprecherin der BMZ Germany GmbH zu einem Besuch einlud. Schnell war ein Termin gefunden, zu dem nicht nur ein Rundgang durch die Produktion, sondern auch ein Informationsgespräch mit dem Brandschutzbeauftragen, Fachkraft für Arbeitssicherheit und gleichzeitig stellvertretender Kommandant der Feuerwehr Gemeinde Karlstein, Herrn Brendel geplant war.
Als Erstes durfte ich mir die Produktion der Batteriespeicher anschauen. Wie in der Elektronikfertigung üblich, muss man sich dazu „ESD*-konform“ kleiden. Einen Schutzkittel anziehen und eine entsprechende Ableitung an den Schuhen anbringen, um statische Aufladung durch Bewegung der Kleidungsstücke zu vermeiden. Elektrische Spannung durch statische Aufladung ist der Tod elektronischer Bauteile, sollte man diese berühren. (*ESD ist Englisch und bedeutet „Electrostatic Discharge“, übersetzt elektrostatische Entladungen).
Es folgte ein ca. einstündiger Rundgang durch die in großen Teilen vollautomatische Produktion von Batteriemodulen. Der hohe Automatisierungsgrad ist gerade bei Produkten, die eine enge Toleranz an Qualitätsmerkmalen haben, sehr wichtig. Zumal hohe Stückzahlen gleicher Baugruppen gefertigt werden. Gleichzeitig ist die Fertigung sehr flexibel aufgebaut, um sich den Anforderungen des Marktes zu stellen und schnell andere Typen von Batterien zu bauen. Eine händische Montage ist zeitaufwändig und relativ teuer. Die BMZ Germany GmbH fertigt allerdings im Bereich der Medizingeräte in kleinen Stückzahlen und Sonderanwendungen auch konventionell.
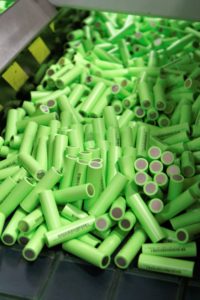
Lithium-Ionen-Zellen 18650
3,65V / 3000 mAh
Foto: Ulrich Wolf
In dem Fertigungsbereich, den ich mir anschauen konnte, werden eigene Terra E-Zellen & zugekaufte Batteriezellen (Lithium-Ionen) in runder, zylindrischer Form vollautomatisch auf Spannung und Impedanz gemessen und mittels Roboter in eine Schablone eingesetzt. Durch den Messvorgang ist sichergestellt, dass nur Zellen montiert werden, die elektrisch in Ordnung sind und auch richtig gepolt eingesetzt werden. Dann erfolgt der nächste Schritt und die Gruppe der Zellen wird in den Zellhaltern verpresst. Diese beinhalten auch den Zellverbinder, dadurch bekommen die Zellen die elektrische Verbindung auf der Unter- und Oberseite. Also den Plus- und Minuskontakt. Anschließend werden die Zellen mit dem Verbinder verschweißt.
Eine solche Baugruppe kann je nach Anwendung eine unterschiedliche Anzahl von Zellen beinhalten, die parallel und seriell verschaltet werden können. Eine Anwendung sind beispielsweise Heimspeicher. Die Batterien der BMZ Heimspeicher sind modular aufgebaut und erweiterbar und somit für den jeweiligen Einsatz als Energiespeicher für eine PV-Anlage auf Wohngebäuden richtig dimensioniert.
Zurück zur Produktion: BMZ fertigt neben eigenen Batterien und Energiespeichern auch OEM-Geräte für Kunden. Vom kleinen, akkubetriebenen Medizingerät über Batterien für Werkzeuge wie Akku-Schrauber oder ähnlich, für Rasenmähroboter und auch Antriebsbatterien für eFahrzeuge. Darüber hinaus gibt es einen Shop für eBikes. Die BMZ-Group hat weltweit Standorte für Produktion, Service und derzeit insgesamt mehr als 2300 Mitarbeiter. Die Website der BMZ-Group zeigt das ganze Leistungsspektrum und weitere, umfassende Informationen zum Unternehmen und zu seinen Produkten.
Eine gebrauchsfertige Lithium-Ionen-Batterien benötigt immer ein so genanntes Batterie-Management-System (BMS).
Diese elektronische Baugruppe sorgt dafür, dass Batterien hinsichtlich Lade- und Entladestrom, Temperaturbereich und weiteren Parametern stets sicher betrieben werden. Das BMS ist teilweise innerhalb der Zellenbaugruppe und/oder innerhalb des Batteriegehäuses verbaut.
Die BMZ Germany GmbH verbaut im Jahr ca. 500 Mio. Li-Ionen Zellen zu vielerlei Arten von Batterien. Damit die Geräte für den Anwender sicher zu verwenden sind, wird an alle Bauteile ein hoher Qualitätsanspruch gelegt und auch in der laufenden Fertigung werden immer wieder Zellen und Batterien gemessen und getestet. Ich konnte mir anschauen, wie ein Mitarbeiter die Festigkeit der geschweißten Kontaktfähnchen mittels Zugtest prüft. Die Zelle wird zwar dabei zerstört, aber ein sicherer Kontakt innerhalb der Batterie ist für die einwandfreie und langlebige Funktion elementar.
Da geladene Lithium-Ionen-Batterien eine hohe Energie in sich tragen und auch chemische Bestandteile besitzen, die gesundheitsschädlich und auch umweltgefährdend sind, wird bei der BMZ Germany GmbH sehr auf Arbeitssicherheit geachtet und der betriebliche, wie auch der vorbeugende Brandschutz haben einen hohen Stellenwert. Alle Mitarbeiter sind umfassend geschult und tragen die erforderliche persönliche Schutzausrüstung.
Beim Umgang mit Batterien kann es zu technischen Defekten kommen und die Zellen können z.B. durch Kurzschluss im Innern mit Rauchentwicklung und auch unter Flammenbildung ausgasen. Zur Früherkennung wird in der Fertigung und im Lager permanent die Raumluft auf Partikel detektiert. Rauchpartikel würden Alarm auslösen.
Sollte an einem Arbeitsplatz eine Batterie rauchen oder brennen, stehen überall Havariebehälter in unterschiedlichen Größen bereit, die ein nichtbrennbares Polstermaterial enthalten und im Anwendungsfall, mit einem Deckel verschlossen und sofort ins Freie gebracht werden.
Hier kann der Behälter zum Löschen des defekten Akkus mit Wasser geflutet werden oder der Akku kann gefahrlos ausbrennen.
Im Lagerbereich sorgt eine automatische Sprinkleranlage für Sicherheit. Teilweise befinden sich über jedem Regalfach Sprinklerdüsen. Zum Löschen wird Wasser verwendet, welches in einem großen Tank mit rund 750.000 Litern Fassungsvermögen vorgehalten wird. Die Lagerhallen sind zur Rückhaltung von kontaminiertem Löschwasser mit wasserdichten Sperren an Türen und Toren ausgestattet, um im Brandfall einen Umweltschaden zu vermeiden.
Am Ende des Rundgangs durch Produktion, Lager und Sprinklerzentrale war noch Zeit für ein sehr informatives Gespräch mit Frau Landgraf und Herrn Brendel. Neben meinen Fragen, die alle kompetent beantwortet wurden, konnte ich mich mit Herrn Brendel zu Löschmethoden, Gefahren und Besonderheiten bezüglich Lithium-Ionen Batterien austauschen. Wir beide besprachen einige Dinge und Ideen, die man hinsichtlich der Gefahrenabwehr bei Lithium-Ionen Batterien verbessern könnte. So zum Beispiel eine Kennzeichnung von Aufstellräumen der Speicher oder eine laienbedienbare Steckverbindung von Speichern, um die Evakuierung im Brandfall durch Einsatzkräfte zu ermöglichen. Herr Brendel betonte, dass Energiespeicher bei entsprechender Wartung und Einhaltung der geltenden Regeln der Technik sicher sind! Brand- oder Schadenfälle sind sehr selten. Erwähnenswert ist noch, dass die Fa BMZ Germany GmbH im August 2022 der örtlich zuständigen Feuerwehr Karlstein einen Abrollbehälter Wanne sponsern konnte. Der AB-Wanne lässt sich vielfältig einsetzen und dient in erster Linie zum Lagern von Flüssigkeiten jeglicher Art. Man kann den Abrollbehälter als Löschwasserpuffer oder zum Kühlen von thermisch beaufschlagtem Brandgut wie Druckgasbehälter oder auch zur Zwischenlagerung von kontaminiertem Löschwasser bis zur Entsorgung einsetzen, wie es in einer Pressemitteilung heißt.
Durch den hohen Qualitätsanspruch an Bauteile und die fertigen Speicher und Antriebsbatterien sind die Produkte, die das Werk verlasen, sicher. Wie ich beschrieben habe, sorgen laufende Kontrollen und Messungen dafür, dass am Ende die Anwender sichere Batterien haben, die die nötigen Normen und Vorschriften erfüllen.
Für das Ende der Lebensdauer ihrer Batterien hält die Fa. BMZ Germany GmbH spezielle Havariebehälter für den sicheren Transport zu einem Entsorgungsdienstleister vor. Somit werden die gesetzlichen Anforderungen erfüllt.
Mein Fazit: Es war ein sehr interessanter und aufschlussreicher Besuch eines innovativen Unternehmens. Der Blick hinter die Kulissen hat mein Wissen um die Technik erweitert und die offene und freundliche Kommunikation empfand ich als sehr positiv.
An dieser Stelle bedanke ich mich ganz herzlich bei Frau Christiane Landgraf, Herrn Martin Brendel, Michael Bihler sowie Christopher Aulbach, die mich durch die Produktion führten!
Link zur Website „Wir über uns“ der BMZ Group